In industrial applications, the strength and toughness of glue often directly affect the structural stability and durability of the product. However, we often encounter such a problem: after curing, the glue becomes hard and brittle, and is prone to cracking or peeling , especially in some application scenarios with concentrated stress.
So, what is the reason for the embrittlement of glue after curing? And how to avoid it? Below we will analyze it in depth from three dimensions: material composition, curing process and modification strategy.
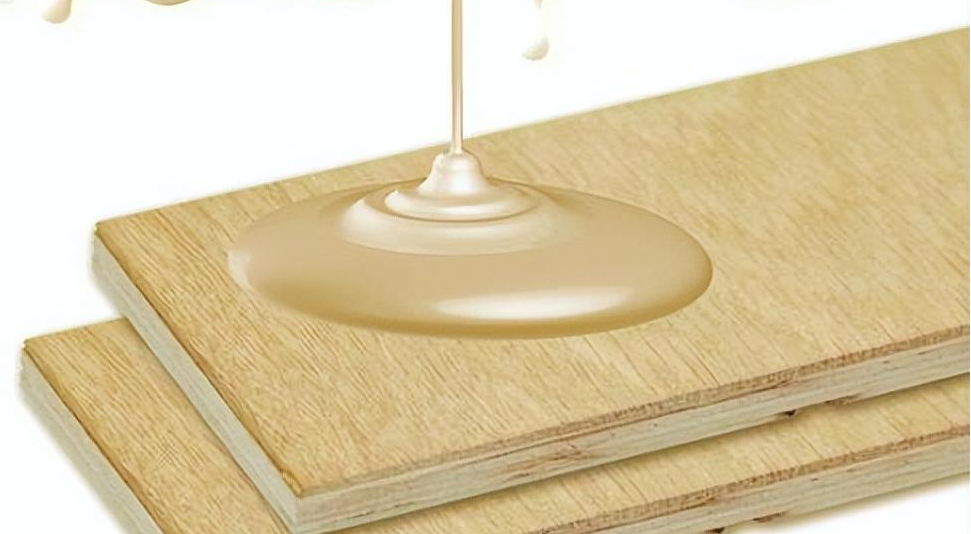
1. The influence of glue composition unreasonable cross linking structure is the root cause
The ingredients of the glue formula directly determine its physical properties after curing.
Some adhesives (such as those containing a large number of hydroxyl groups or rigid segments) form a dense three-dimensional network structure through cross-linking agents during the curing process. Although they can provide a certain strength in the early stage, this high cross linking density structure usually lacks flexibility and is very easy to break under stretching or impact .
Common causes include:
- Uses a rigid structure based main chain monomer (such as an aromatic ring structure)
- The cross-linking agent ratio is too high , resulting in a lack of elastic adjustment space inside the glue layer
- Lack of toughening agents or flexible segments
Improvement direction : Choose elastic systems such as polyurethane, epoxy or modified silicone adhesives, which are more suitable for bonding scenarios that require toughness.
2. Impact of the curing process: Improper temperature/speed control will increase brittleness
Even if the formula is reasonable, if the curing process is not properly controlled, it can easily lead to the phenomenon of “hard surface and brittle inside” or “insufficient cross-linking”.
- Curing too quickly : The surface of the glue reacts quickly to form a film under high temperature or high catalytic concentration, but the interior has not yet been fully cross-linked, resulting in stress concentration and brittle cracking risks.
- Low environmental humidity or large temperature difference : affects the diffusion of reactants and the uniformity of cross-linking, and is prone to produce brittle cracking points.
Improvement direction :
- Control the curing temperature and time to make the reaction mild and sufficient
- Use a suitable curing agent to avoid too fast reaction rate
- Curing in an environment of room temperature + moderate humidity, heating and insulation to slow curing if necessary
3. Modification methods: increasing toughness and crack resistance
In order to fundamentally improve the flexibility and durability of the cured adhesive layer, the following modification methods can be introduced:
Add elastomer or flexibility enhancer
Such as: polyether polyols, TPU particles, liquid nitrile rubber, etc., can improve the elongation at break and impact resistance of the rubber layer.
Add antioxidants or UV stabilizers
Suitable for outdoor environment applications, it can delay the aging process and avoid late brittle cracking due to structural degradation.
Compound multi stage structure main agent
For example, a two-component polyurethane system with a collaborative design of “hard segment + soft segment” can maintain structural strength while also having good toughness.
Conclusion
It is not accidental that the glue becomes brittle after curing, but the result of multiple factors such as formula design, curing process and use environment.
By rationally selecting materials, optimizing processes and modifying formulas , the occurrence of brittleness problems can be effectively avoided, ensuring the service life and structural safety of the product.
If you encounter problems with poor glue curing performance, insufficient strength, or brittle cracking in your project, please contact us and we can provide you with a more suitable glue solution.